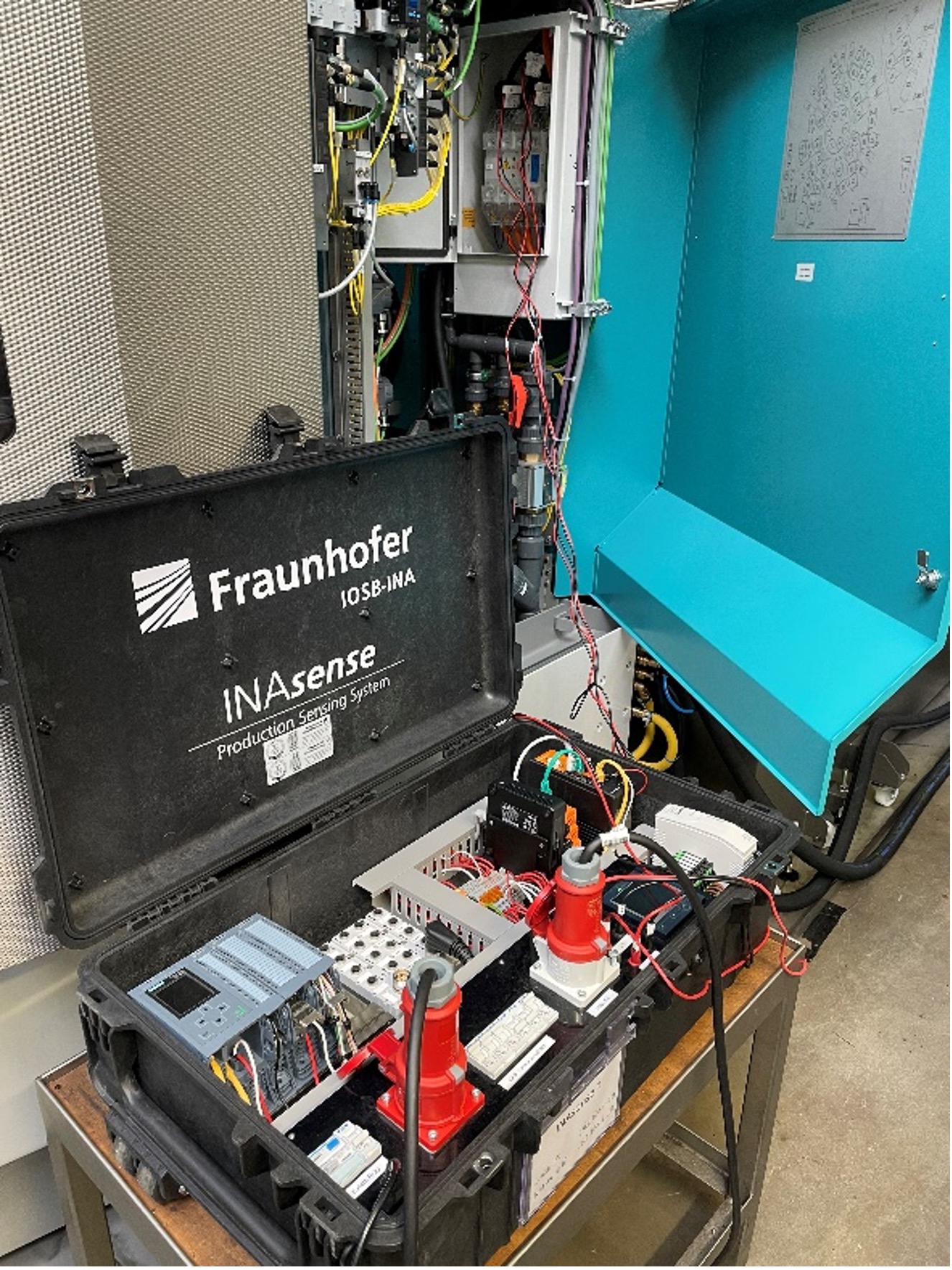
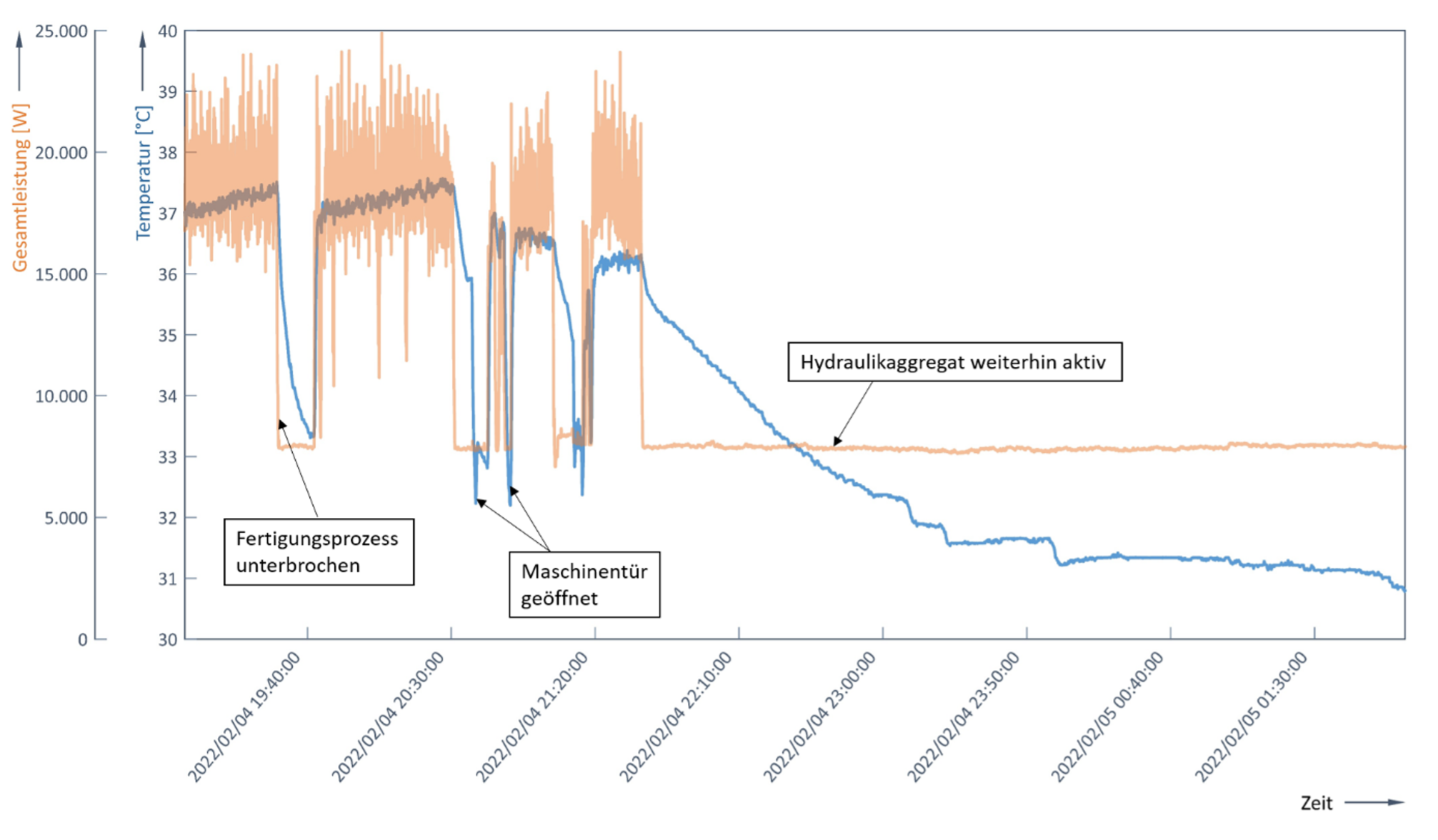
Die Ausgangssituation:
Die Bundesregierung hat ihre Ziele im Rahmen der Änderung des Klimaschutzgesetzes 2021 deutlich verschärft. Demnach sollen im Jahr 2030 die Treibhausgasemissionen um 65% gegenüber 1990 gesenkt werden. Der Industriesektor und insbesondere produzierende Unternehmen können über die Senkung von Energieverbräuchen, Steigerung der Energieeffizienz und den Einsatz erneuerbarer Energien substanziell zu den globalen und nationalen Klimaschutzzielen beitragen.
Die Herausforderung:
Um sowohl die Klimaziele bei gleichzeitigem Erhalt der Wettbewerbsfähigkeit einhalten zu können, als auch den durch die aktuelle Energiekrise ausgelösten steigenden Energiekosten zu entgegnen, müssen kurzfristig und verstärkt Potenziale zur Energieoptimierung erkannt und genutzt werden.
Sensordaten-basierter Energiespar-Service von Fraunhofer IOSB-INA:
Um Ihrem Unternehmen einen einfachen Zugang zu Energiedaten an Maschinen und Anlagen im Rahmen von Potenzialanalysen zu bieten, nutzen wir unsere skalierbaren Produktionsdatenerfassungssysteme. Diese beinhalten Energiemessgeräte, welche Energiedaten ohne einen signifikanten Eingriff in die Elektroinstallation der Maschinen erfassen können. Für die Energiemessungen sind lediglich ein Zugang zu den drei Phasen der Maschinenstromzufuhr sowie eine Referenzspannung über eine CEE-Steckdose erforderlich. Die erfassten Energiedaten können im Verbund mit optional weiteren Sensordaten lokal oder in der Cloud gespeichert und visualisiert werden. Somit bietet sich die Möglichkeit, über einen bestimmten Zeitraum (z.B. eine Woche) ununterbrochen Produktionsdaten zu erfassen, Ihnen diese auf einem Dashboard anzuzeigen und zu speichern. Im Anschluss an die Messkampagne modellieren und klassifizieren Fraunhofer-Forscher die Daten. Hieraus können für das Unternehmen energetische Fußabdrücke generiert werden. Eingestellte Soll-Werte können mit dem Energieverbrauch und dem Produkt zusammengebracht werden. Es ergibt sich dann die Möglichkeit, dem Unternehmen im Livebetrieb Vorschläge zu unterbreiten wie die aktuelle Produktion angepasst werden kann, um einen historisch bekannten Fußabdruck zu erreichen, der durch Rohstoffänderungen oder Veränderungen in den Produktionsbedingungen aktuell nicht erreicht werden kann. Unternehmen erhalten zudem den OEE-Wert ihrer Maschine(n) sowie gegebenenfalls wichtige Hinweise auf erkannte Anomalien im Produktionsprozess.
Unser Angebot:
- Temporäre Energiemessung an Maschinen und Anlagen im Verbund mit optionaler zusätzlicher Prozessdatenerfassung durch überwiegend kontaktlose Sensoren mit unseren skalierbaren Produktionsdatenerfassungssystemen
- Visualisierung der Live-Daten vor Ort und / oder im Intranet auf einem Dashboard
- Speicherung der Daten entweder lokal oder falls gewünscht auf Fraunhofer-Cloud-Server
- KI gestützte Daten-Klassifikation im Hinblick auf den energetischen Fußabdruck
- Auswertung der Abweichung einer aktuellen Produktion mit Hinblick auf eine vergleichbare Produktion und Erstellung einer Maßnahmenhypothese zum erreichen eines energetisch optimaleren Zustandes der Produktion.
- Herstellen einer OEE-Transparenz zur Identifikation von energetischer Verschwendungen rund um den Produktionsprozess und in Stillstandzeiten der Maschine
- Aufzeigen auftretender energetische sowie prozesstechnischer Anomalien im Produktionsprozess
- Untersuchung der Produktionsumgebung auf thermische Hotspots mittels Infrarotkamera
- Einbezug peripherer Aggregate wie Druckluftkompressoren oder Trocknungsmodulen anhand der Energiedaten
- Unterstützung beim Aufbau eines zentralen Energiecockpits auf einer selbst betriebenen oder in der Cloud gehosteten Datenplattform
- Implementierung KI-basierter Softwarelösungen zur Erhöhung der Energieeffizienz (z.B. in Form einer Anlagen-übergreifender Energieoptimierung, einer energieeffizienten Auftragsplanung und einer intelligenten Ansteuerung elektrischer Antriebe)
- Umsetzung eines ECO-Modes für Maschinen und Anlagen
- Vorbereitung und Durchführung weitergehender Maßnahmen im Rahmen von Industrie 4.0 Retrofits
Das Einsparpotenzial im Beispiel:
Am Beispiel einer Zerspanungsmaschine in einem produzierenden Unternehmen zeigte das Fraunhofer IOSB-INA anhand einer Energiedatenerfassung und –analyse (siehe Abbildung 1) exemplarisch auf, dass nach Schichtende Hydraulikpumpen nicht abgeschaltet wurden und außerhalb der Arbeitszeiten eine Leistungsaufnahme von ca. 7,2 kW pro Maschine gemessen wurde (siehe Abbildung 2). Bei angenommenen Stromkosten von 50 Cent/kWh entstanden dem Unternehmen je nach Anzahl der Arbeitsschichten somit pro Jahr und Maschinenkosten von ca. 7.400 € bei einem 3-Schichtbetrieb gemäß IG-Metall-Tarif bzw. 24.300 € bei einem 1-Schichtbetrieb mit jeweils 8 Stunden werktags.
Weiterführende Informationen und Referenzen:
Friesen, Andrej; Flatt, Holger; Jasperneite, Jürgen: Leitfaden Retrofit für Industrie 4.0 - Neuer Nutzen mit vorhandenen Maschinen. In: VDMA Forum Industrie 4.0, Frankfurt am Main, Nov. 2020.
Schulte, Bastian; Flatt, Holger; Schulte, Reinhold; Kleinhans, Chris: Automatisierte Qualitätskontrolle: Retrofit für Bestandsanlagen. atp magazin 08/2022, S. 46 ff, 2022.
Firma Weier: Potentialanalyse für Drehmaschinen. In: it’s owl, Projektwebseite, 2021
Firma Weier: Umsetzung eines permanenten Retrofits für eine Drehmaschine. In: it’s owl, Projektwebseite, 2021
Firmen Bosch Rexroth und Friedrichs & Rath: Umsetzung von Praxisbeispielen zum Thema Industrie 4.0 Retrofit. In: VDMA Leitfaden Retrofit für Industrie 4.0, 2020
Firma Miele & Cie. KG: In: Digital Manufactoring Magazine, Projektwebseite, 2015
Innovationsprojekt „Maschinelles Lernen für die Produktion und deren Produkte (ML4Pro²)“, In: it’s OWL, Projektwebseite, 2022
Innovationsprojekt „Intelligente Antriebs- und Steuerungstechnik für energieeffiziente Intralogistik“. In: it’s owl, Projektwebseite, 2017
IGF-Projekt „Analyse und Überwachung des Energieverbrauchs in der Verfahrenstechnik und der Produktionstechnik“. In: IMMS, Abschlussbericht, 2014